技術力と粘り強さで乗り越えた
“1台に3台分の機能”という
前例のない挑戦

半導体製造に欠かせない
ガス流量制御器FCS-P8500
「1台で3台分の機能を」――。2016年、開発チームは一つのミッションへの取り組みを始めました。半導体の製造に必要な「ガス流量制御器」の新製品開発です。開発が成功すれば、半導体装置メーカーにコスト削減をもたらす魅力的な製品となります。しかし、開発の道のりは険しく、問題を解決できずに一度は諦めそうになりました。開発メンバーは「挑戦したのは、1台の車を運転手2人で走らせるようなものでしたから」と振り返ります。正式なリリースまでに費やした期間は約4年。どのような困難を、どのように乗り越えたのでしょうか。開発の経緯をたどります。
MEMBER
-
技術統括
N -
開発リーダー・
ハード
設計
H -
ソフト設計
S -
アプリ設計・
試作評価
O
Chapter 1
半導体の進化から生まれる
新たなニーズ

ラインは増やせない。
それなら、3台の機能を1台に
詰め込めないか。
半導体はスマートフォンや家電、自動車など身の回りのあらゆる電気製品に使われ、私たちの暮らしに欠かせない存在になっています。
その半導体は、半導体製造装置でたくさんの工程を経てつくられます。直径30cmの基板の表面に膜を作る「成膜」や、その膜を除去して回路パターンを生成する「エッチング」などの工程では、さまざまな種類のガスが使われます。
この時に必要になるのがガス流量制御器です。半導体はナノメートル(1mmの100万分の1)レベルの微細な構造をしているため、製造装置内で使うガスの量は非常に高い精度でコントロールされなければなりません。
Point 「ガス流量制御器」
半導体製造装置内のガスを流す量をコントロールする装置。サイズは規格で決まっている。ガスの量がきちんとコントロールできていないと、半導体の品質がばらつく原因になる。通常、複数種類のガスを使ううえ、同一のガスで使用量の幅が大きい場合があるため、ガス流量制御器も複数台が必要になる。
成膜やエッチングなどの工程は、ガスの種類と流量を高精度かつ短時間に次々と切り替えて行います。このため、小さい量から大きな量まで高精度にガスを流せるガス流量制御器が必要になります。
フジキンは、FCS-P7000シリーズなどで半導体装置メーカーであるお客様のニーズを満たしてきました。ところが、新たなニーズが生じます。ガスの多様化です。
半導体は微細化が進むなど日々進化し、製造工程も改良されています。そのため、「新しい種類のガスを流したい」といったニーズや、異なる流量に対応する必要が生じます。しかし、新たに流量制御器を増設できない場合があります。
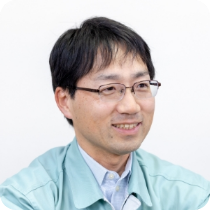
開発リーダー・ハード設計 H
チャンバーにガスを供給するラインは16系統が標準的です。
16系統を目いっぱい使っていたらもう増やせません。改造は困難です。
新製品の用途
半導体製造プロセスにおける流量制御器
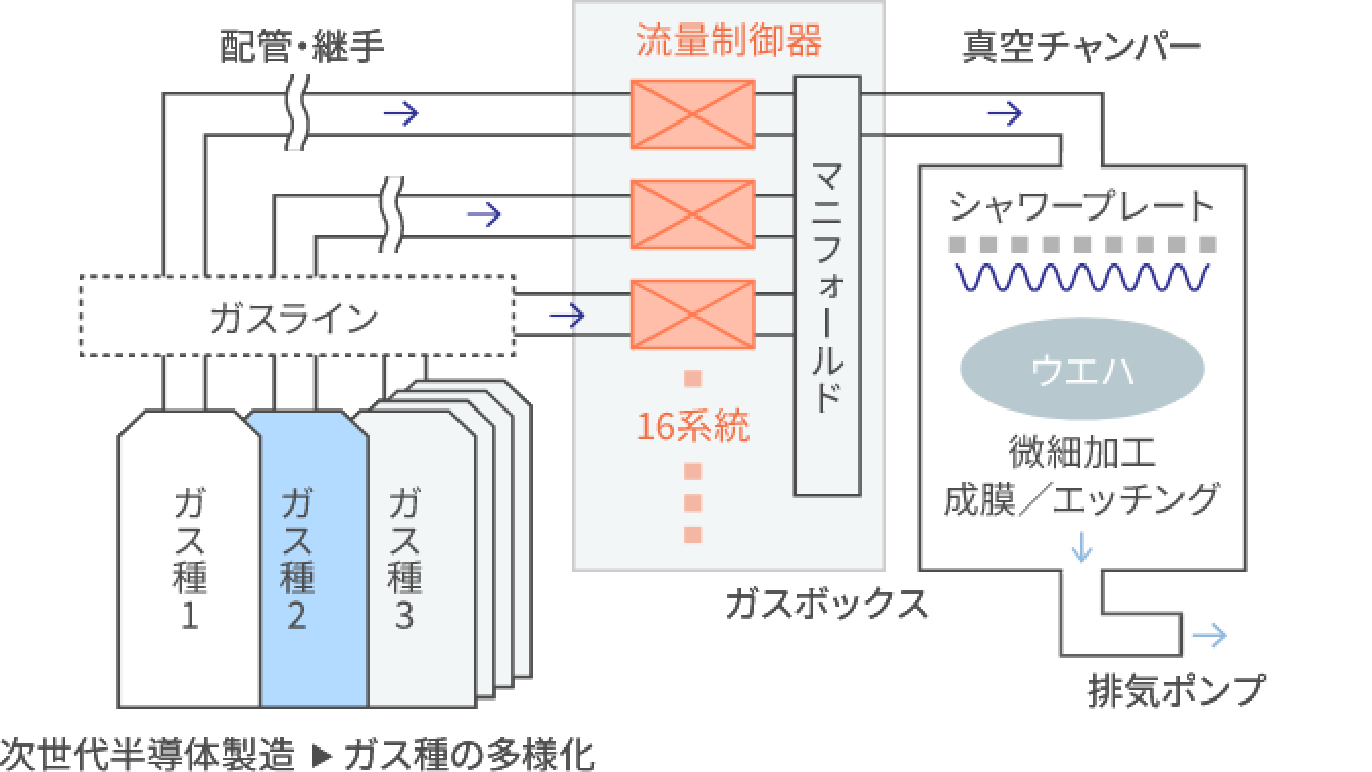
開発成果
流量制御器の小型化に成功(サイズ1/3)
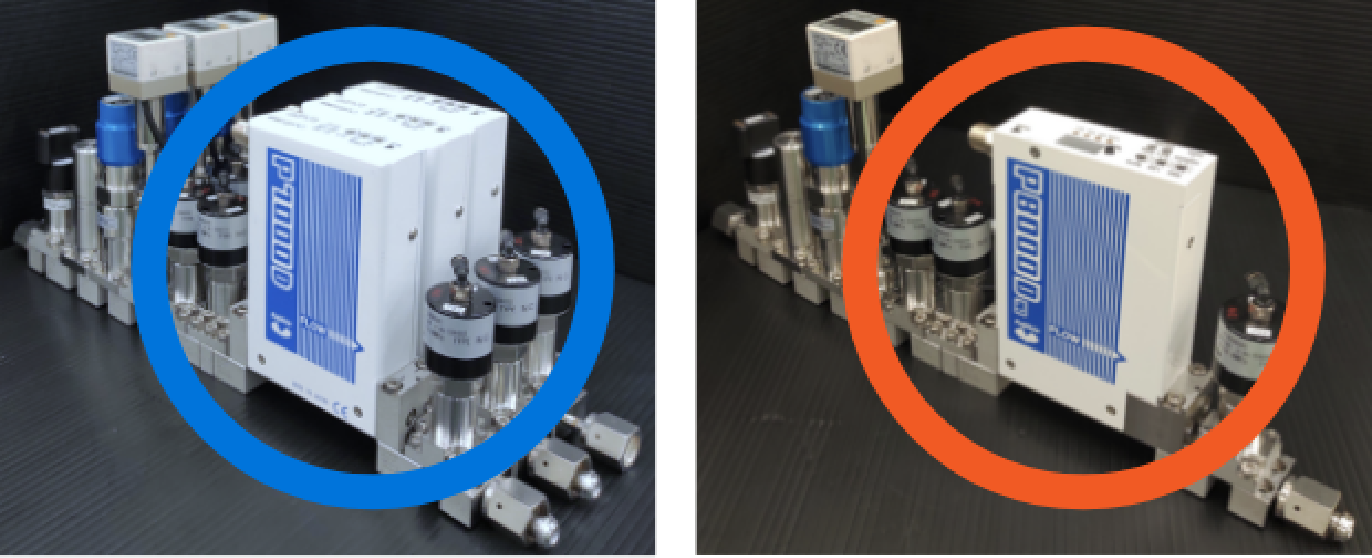
そこで、「流量の範囲を広くして、3台の流量制御器を1台にできないか」という発想が社内から出てきました。
これは、1種類のガスのために3機種を設置しているケースがあるためです。流量制御器は、コントロールできる流量の範囲が機種ごとに決まっています。同じガスでも、使う量を毎分1~1000cm³の範囲で変化させなければならない場合は、流量が毎分1~10cm³、毎分10~100cm³、毎分100~1000cm³の3機種が必要でした。
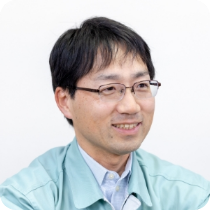
開発リーダー・ハード設計 H
例えば、酸素ガスはクリーニング工程では大量に使う一方、膜を削るエッチング工程では非常に小さい量を高い精度で制御しなければなりません。
この場合、限られた16ラインのうちの3ラインを酸素用の装置が独占することになります。この3ラインを1ラインにできたら、2つ分が空いて新しいガスや異なる流量のラインを入れることができます。メーカーにとって大きなメリットです。
Chapter 2
課題が浮き彫りとなった
プロトタイプ
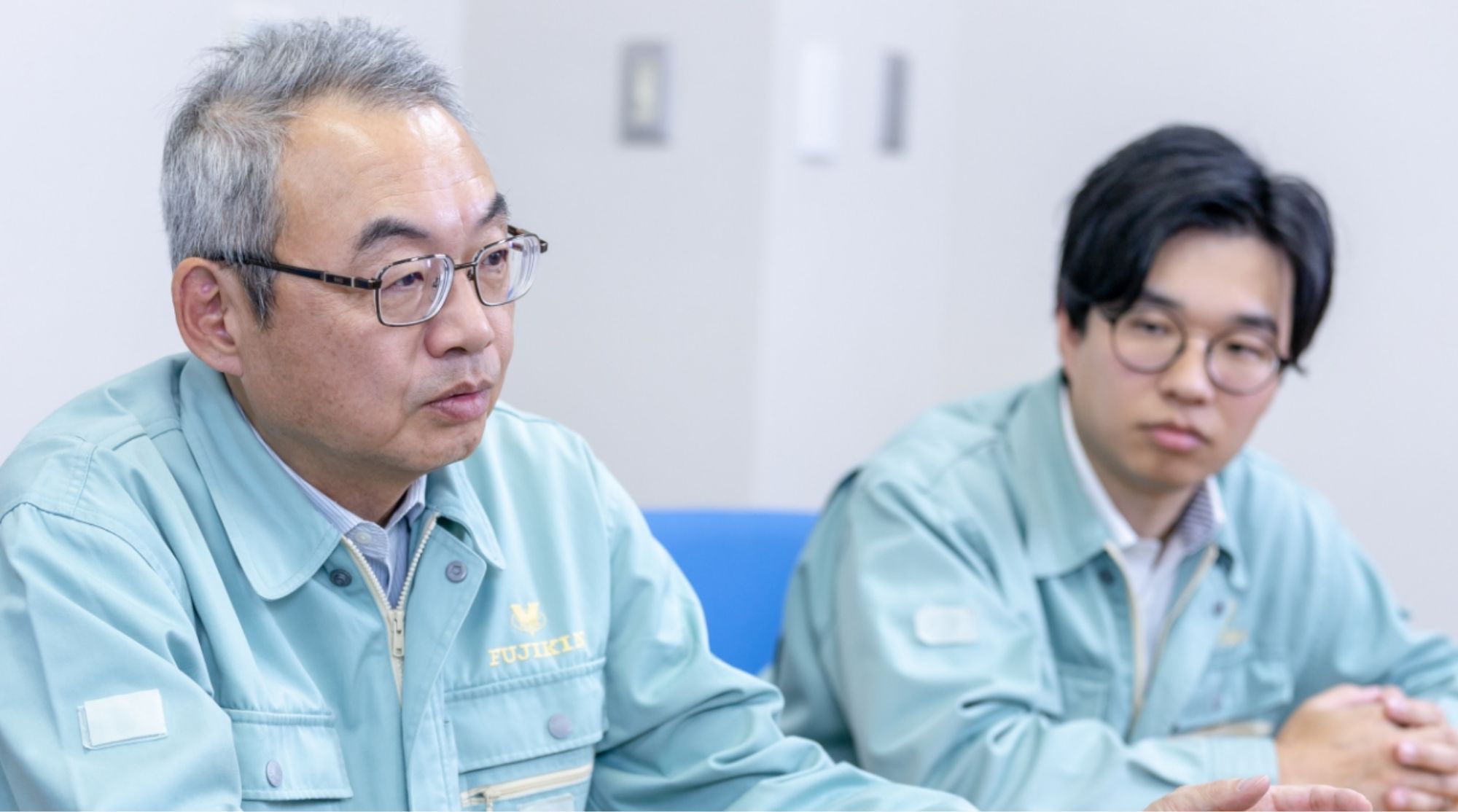
ガス流量の乱れを解消することが、
最優先の課題に。
そこで、従来製品であるFCS-P7000をベースに、流量の範囲を広げた製品を開発しました。のちのFCS-P8500開発へとつながるプロトタイプです。1つの流量制御器の中に大流量用と小流量用の2つの流路(ガスの通り道)を入れ、単純にバルブで切り替える仕組みです。完全には3機種分の流量範囲をカバーすることはできませんが、大きなメリットが得られます。
しかし、このプロトタイプは、性能に改善すべき点が残されていました。切り替え時に、流量がガクンと下がる「アンダーシュート」や急激に上がる「オーバーシュート」などの乱れが生じるのです。
半導体製造でガス流量が乱れると、品質がばらつく原因となってしまいます。流量をいかにオーバーシュートやアンダーシュートなく制御するか。これが重要な課題でした。
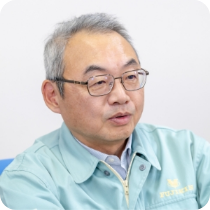
技術統括 N
採用していた装置メーカーからの強い要望もあり、当時は最優先の開発テーマとなっていました。
Chapter 3
蓄積した技術力を生かし、
コンパクト化に成功
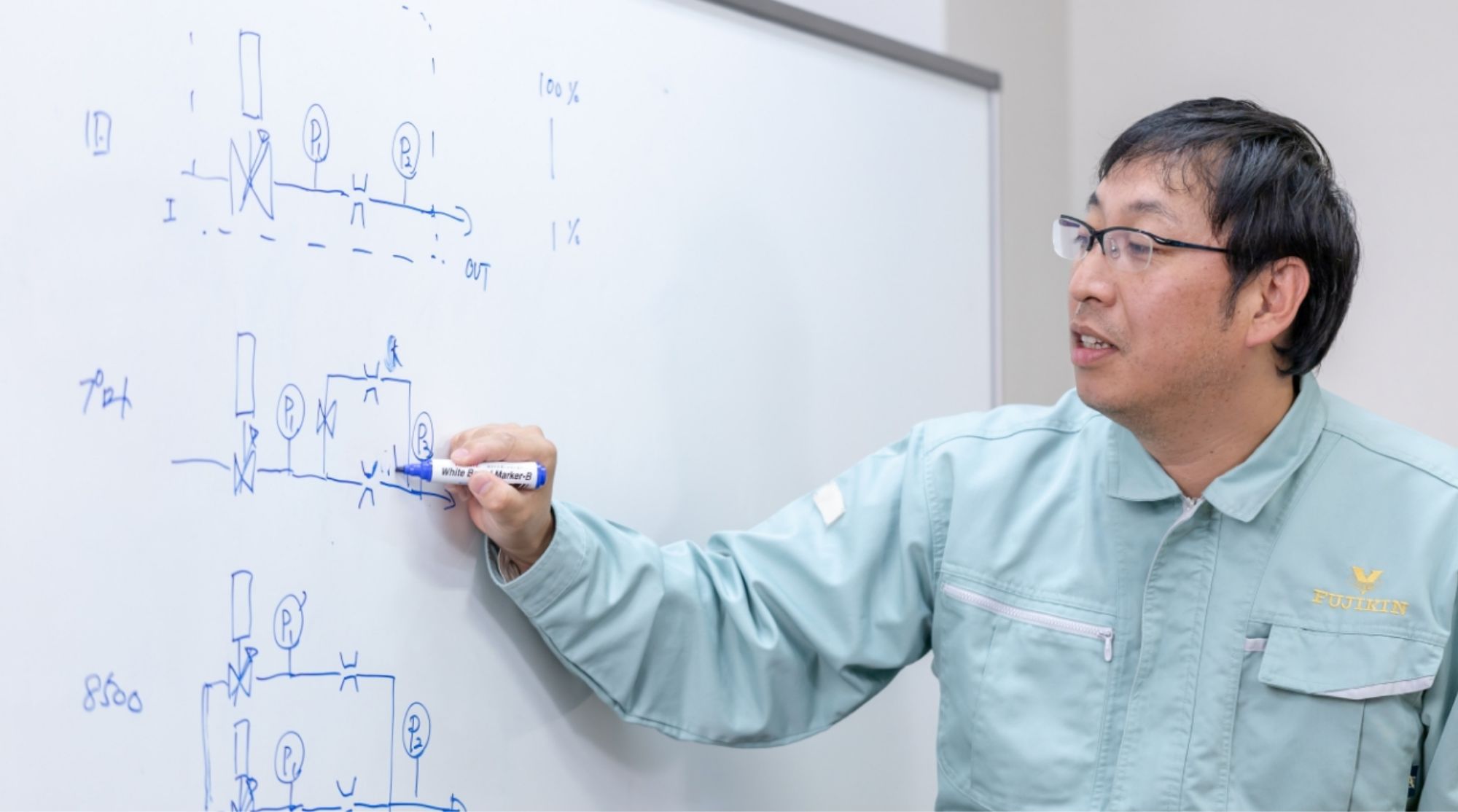
各流路に圧力センサーとバルブを取り付ける。これが突破口に。
2016年11月、新製品の開発がスタートしました。
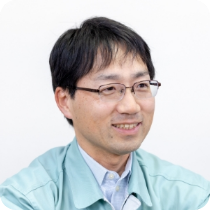
開発リーダー・ハード設計 H
課題を解決できる方法を思いついたので装置メーカーに提案したところ、「それはいいね」という反応でした。このため、製品化に向けて取り組みを始めました。
その解決方法とは――。
1台の中に大流量と小流量の2つの流路を入れるのはプロトタイプと同じですが、それぞれの流路に圧力センサーとバルブを付け、流量を制御できるようにすることでした。
また、流量制御の性能を向上させることによって、2つの流路を内蔵すれば約3台分の流量範囲をカバーできるめども付けられました。
FCS-Pの構成比較表
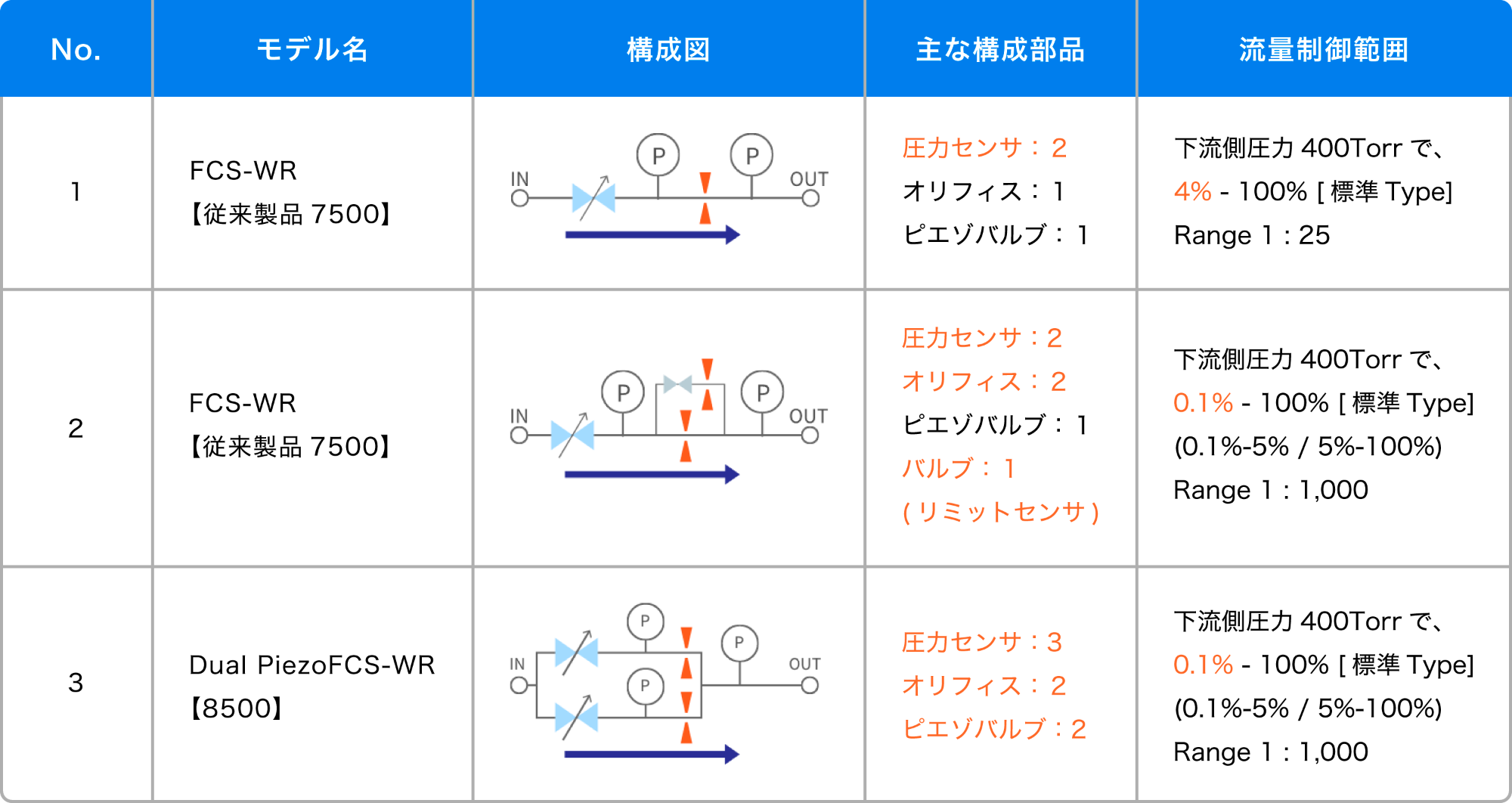
※P:圧力センサー
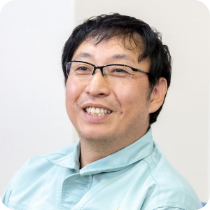
ソフト設計 S
大流量から小流量に切り替える時は、大流量のバルブをゆっくり閉めると同時に小流量のバルブをゆっくり開けるようにしました。プロトタイプは、大流量と小流量をバルブで切り替えるだけだったので、切り替え時に流量が乱れていたわけです。
2台分の部品を1台に納める、という発想
装置2台を1台にする。アイデアは単純かもしれませんが、これまで他にそのような製品がなかったことが実現の難しさを示しています。流量制御器は片手に載る大きさです。ただでさえコンパクトに部品が納められているのに、全く同じ大きさの筐体に2台分の部品を詰め込まなくてはなりません。
まず、開発メンバーのH(開発リーダー・ハード設計)が、4つの圧力センサーと2つのバルブ、そして2つの流路を組み込むことに取り組みました。流路の構造を新たに考え、部品の配置を工夫する。誰も実現していないことへの挑戦です。
支えになったのが、フジキンが培ってきたバルブやシールなどの技術力です。現在の技術だけでなく、過去の技術も掘り起こして設計に利用しました。また、社内でさまざまな装置を開発する中で、部品の小型化が進められていたことも助けになりました。
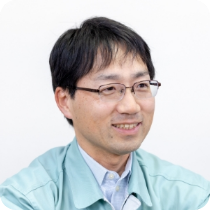
開発リーダー・ハード設計 H
例えば、酸素ガスはクリーニング工程では大量に使う一方、膜を削るエッチング工程では非常に小さい量を高い精度で制御しなければなりません。
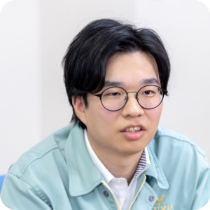
アプリ設計・試作評価 O
全部が納まっているのを最初に見た時は感動しました。 これすごいな、本当に入っている、って。
この場合、限られた16ラインのうちの3ラインを酸素用の装置が独占することになります。この3ラインを1ラインにできたら、2つ分が空いて新しいガスや異なる流量のラインを入れることができます。メーカーにとって大きなメリットです。
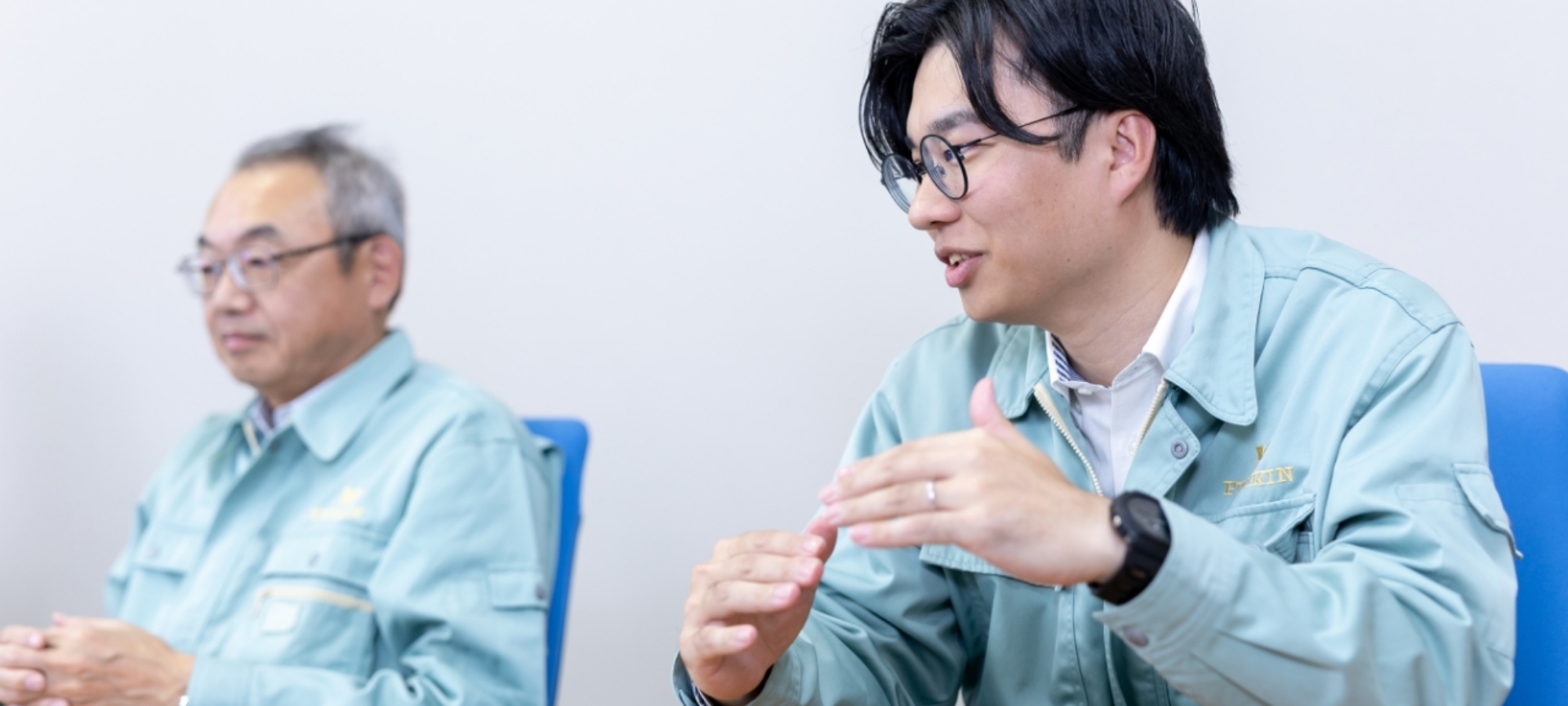
“基板も小さく”は必然に
部品や流路に加え、電子回路の基板も2台分が必要です。これはS(ソフト設計)が担当しました。
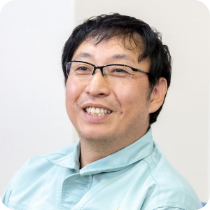
ソフト設計 S
大流量から小流量に切り替える時は、大流量のバルブをゆっくり閉めると同時に小流量のバルブをゆっくり開けるようにしました。プロトタイプは、大流量と小流量をバルブで切り替えるだけだったので、切り替え時に流量が乱れていたわけです。
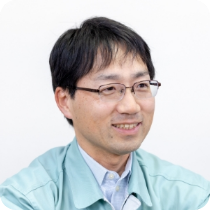
開発リーダー・ハード設計 H
チャンバーにガスを供給するラインは16系統が標準的です。
16系統を目いっぱい使っていたらもう増やせません。改造は困難です。
Chapter 4 最大で最後の難関、ソフト開発
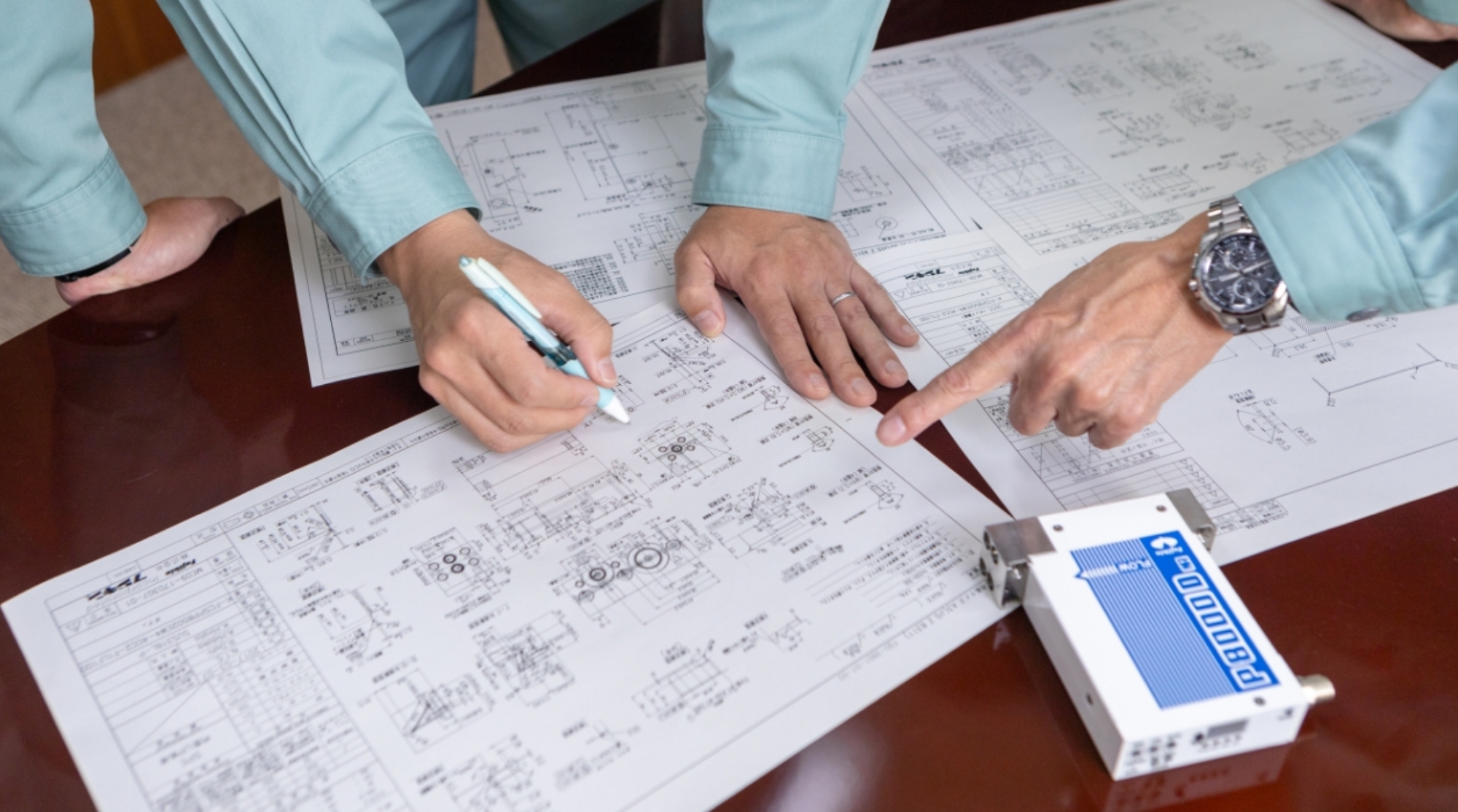
プログラムを工夫し何度も試すが、
目標には届かず。
2台分の部品を1台の筐体に納めることに成功し、あとは大流量と小流量の装置を切り替えるためのソフトウェア開発を残すのみ。担当はS(ソフト設計)とO(アプリ設計・試作評価)の2人です。開発チームは当初、難しくはないと楽観していましたが、大きな間違いでした。
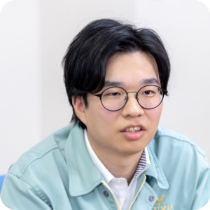
アプリ設計・試作評価 O
コンセプトの段階では「こう制御したらできるはず」って言われましたが、ソフト開発の段階になって実際にプログラムを作ってみたらできないんです。ハードはできていたので、「ソフトが原因で失敗する訳にはいかない」というプレッシャーを感じました。
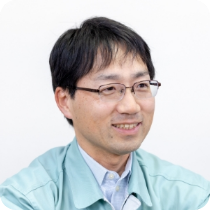
開発リーダー・ハード設計 H
初めは「いけるんじゃないかな」と考えたのですが、全然ダメでした。一方をゆっくり閉めて、もう一方をゆっくり開けて、と言うのは簡単ですが、実際には非常に難しい。
とても苦しい時期が始まりました。
大流量と小流量の両方の流路をガスが流れているため、切り替え時はそれぞれのバルブを制御して流量の合計を滑らかに変化させる必要があります。2秒以内の切り替えが目標でしたが、いくらプログラムを工夫しても滑らかな切り替えに10~20秒もかかってしまいます。
この難しさを理解するため、運転手が2人いる自動車を想像してみてください。
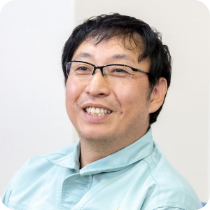
ソフト設計 S
大流量から小流量に切り替える時は、大流量のバルブをゆっくり閉めると同時に小流量のバルブをゆっくり開けるようにしました。プロトタイプは、大流量と小流量をバルブで切り替えるだけだったので、切り替え時に流量が乱れていたわけです。
「運転手」が、ガス流量制御器ではバルブを開け閉めするプログラムに相当します。従来は、1つのバルブを操作して流量を変えればよかったのですが、バルブが2つになった途端に非常に複雑になりました。2つのバルブをうまく連携させ、合流したガスの量を滑らかに変化させるのは至難の業。光が全く見えない状況が続きました。
Chapter 5
突き返された「妥協案」。
半年の試行錯誤
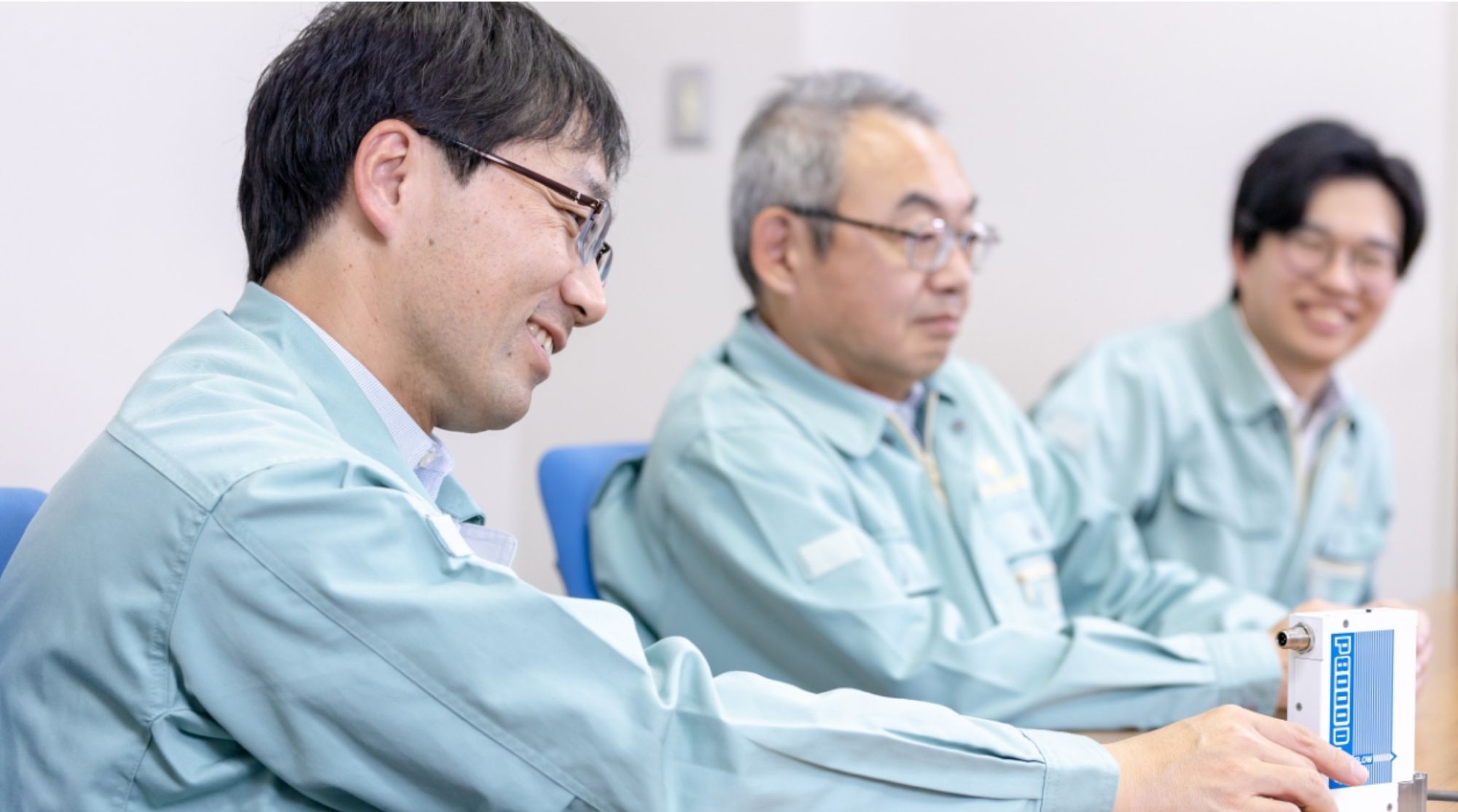
粘り強く、一つ一つ。試行錯誤の末、やっと “答え”を手に。
開発チームは2017年秋ごろ、滑らかな切り替えを実現できないまま中間報告となる、言わば「妥協案」を装置メーカーに示します。
しかし、お客様は受け入れませんでした。
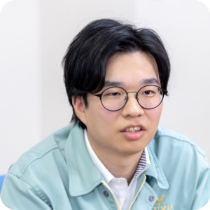
アプリ設計・試作評価 O
利用可能な流量の範囲が広くなるからといって、従来より性能が劣る部分があっていいわけではない。そういう声をいただきました。
開発チームは再びソフトウェア開発に立ち向かいました。メンバーでアイデアを出し合い、粘り強く一つ一つ試してプログラムの改良を試みます。バルブを動かす速度をどのように調整するか、流量センサーの値の変化にどのように対応させるか――。この時に行った作業は、料理のレシピづくりに似ています。
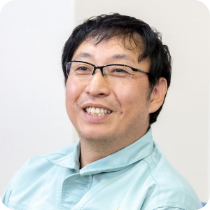
ソフト設計 S
理想どおりの料理を完成させるためには、どういう具材や調味料をどのタイミングでどれだけ入れるか、という調理手順や分量を決めなければなりません。微妙な調整をするのですが、組み合わせが無限にあるため「答え」を見つけるのが非常に難しいんです。
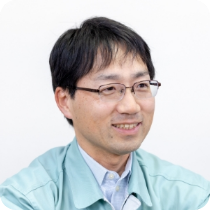
開発リーダー・ハード設計 H
塩加減を調整したり、新たなスパイスを入れてみたり、あらゆることを試して、ようやくレシピを見つけ出した、という感じです。
試行錯誤を重ねること半年。ついに2秒以内で滑らかに切り替えることに成功しました。その時のことを、開発メンバーはよく覚えています。
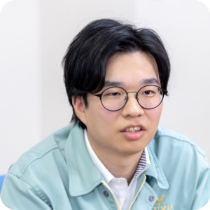
アプリ設計・試作評価 O
H(開発リーダー・ハード設計)さんも一緒にクリーンルームで実験してくれて、やっとのことで答えにたどり着きました。
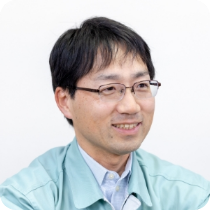
開発リーダー・ハード設計 H
クリーンルームで、思わず「やった」と声が出ました。自分が担当したハードウェア設計よりも、このソフトウェア開発の苦労の方が印象に残っています。とても悩んでいたからでしょうね。
Chapter 6
開発から4年、
量産機を正式リリース
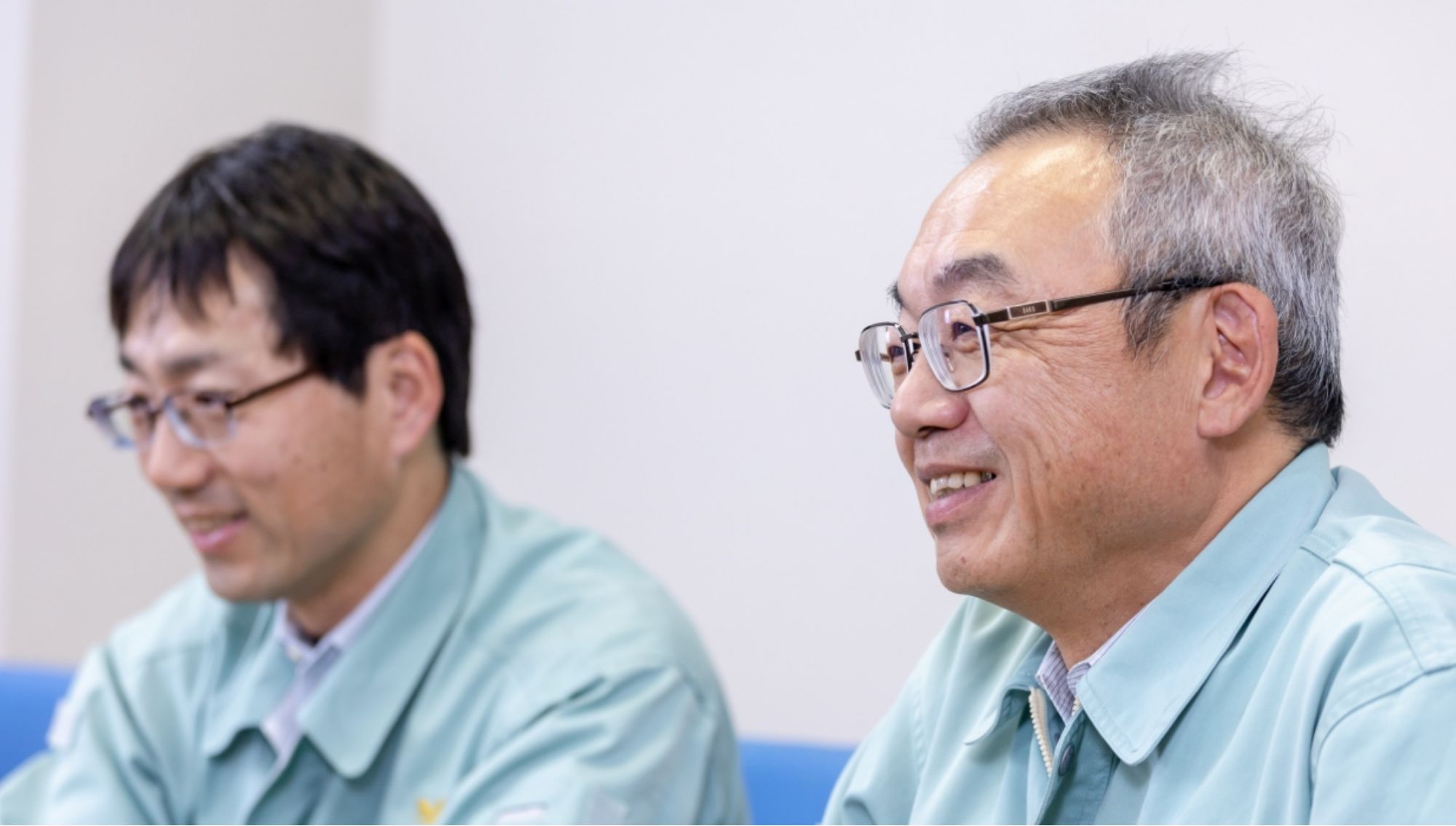
ニーズが続く限り、
私たちの開発は終わらない。
従来機種と比べて遜色ないレベルの性能を実現し、2018年2月に装置メーカーにサンプル出荷をしました。
2020年12月に量産機の正式リリースを果たし、2021年には第18回超モノづくり部品大賞(モノづくり日本会議・日刊工業新聞社主催)の機械・ロボット部品賞に輝きました。
2021年 第18回 超モノづくり部品大賞「機械・ロボット部品賞」受賞の詳細はこちら
流量制御器のサイズは規格で決まっているため、他社製品と簡単に入れ替えられるという厳しい競争にさらされています。そんな中、1台で従来製品3台分の機能を持つFCS-P8500は、半導体製造装置の設計やコスト面で優位に立っています。
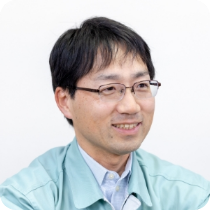
開発リーダー・ハード設計 H
出荷台数が何十台、何百台と伸びていって、うれしかったですね。完成した時は「うれしい」という感じはあまりしませんでしたが、具体的な数を聞いて実感が湧きました。
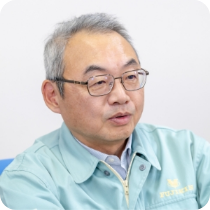
技術統括 N
今後は、お客様がさらに高性能化を求めてくるはずです。「応答速度を速くする」「流量の精度を高くする」などが考えられます。その要求に応えれば採用してもらえる可能性は高く、競合との差別化が図れます。まだまだガス流量制御器の開発は続きます。
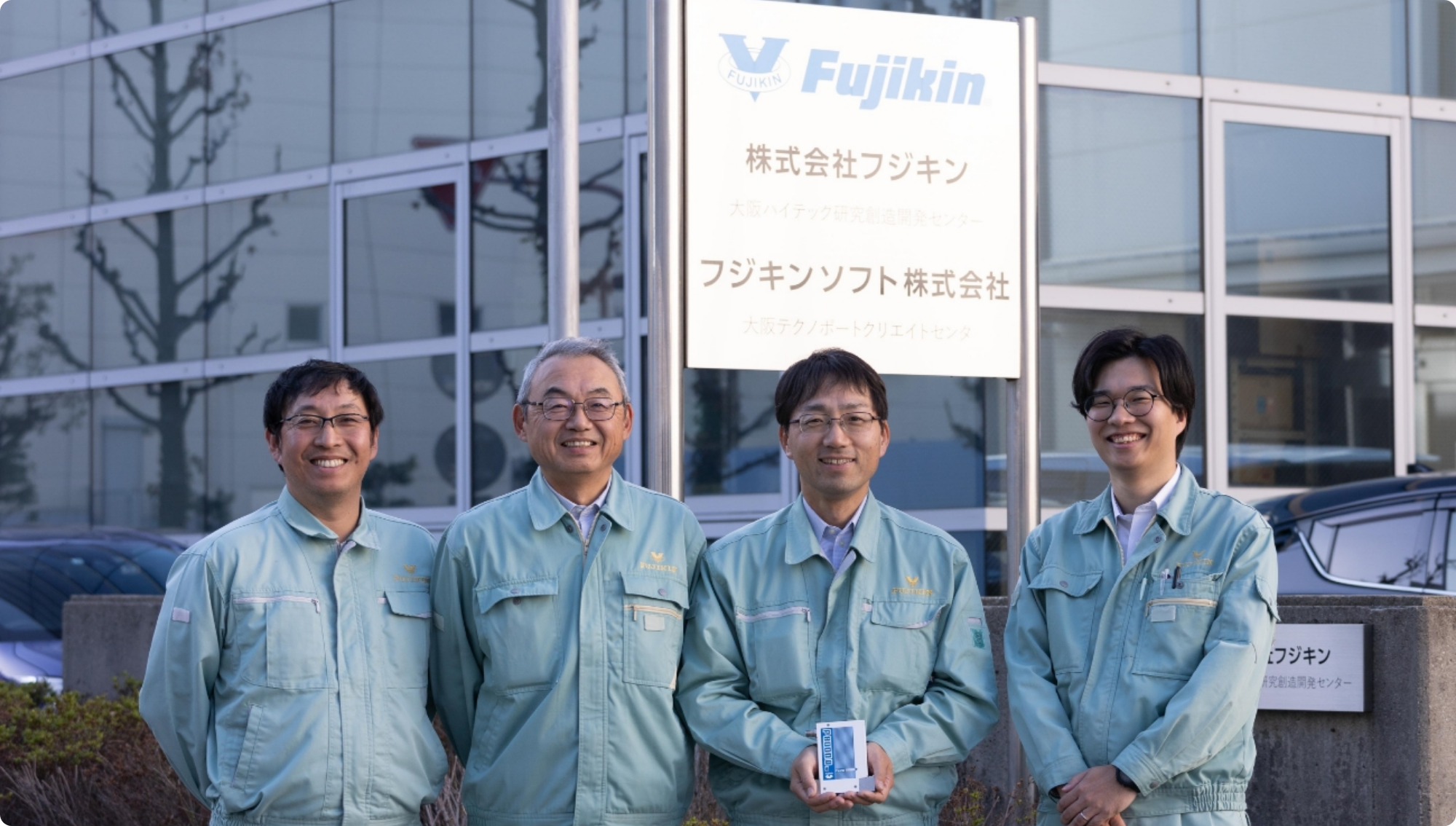
※取材内容、および登場する社員の所属はインタビュー当時のものです。
技術統括 N
フジキンには、2000年に製品化した「FCS-P7000シリーズ」というガス流量制御器があります。当社の従来製品のマスフローコントローラとは原理が異なり、気体の圧力を制御することによって高精度な流量制御を可能にしました。当時の開発は、私が指揮を執っていました。