水素社会の発展を見据え、
新型バルブの開発に挑む
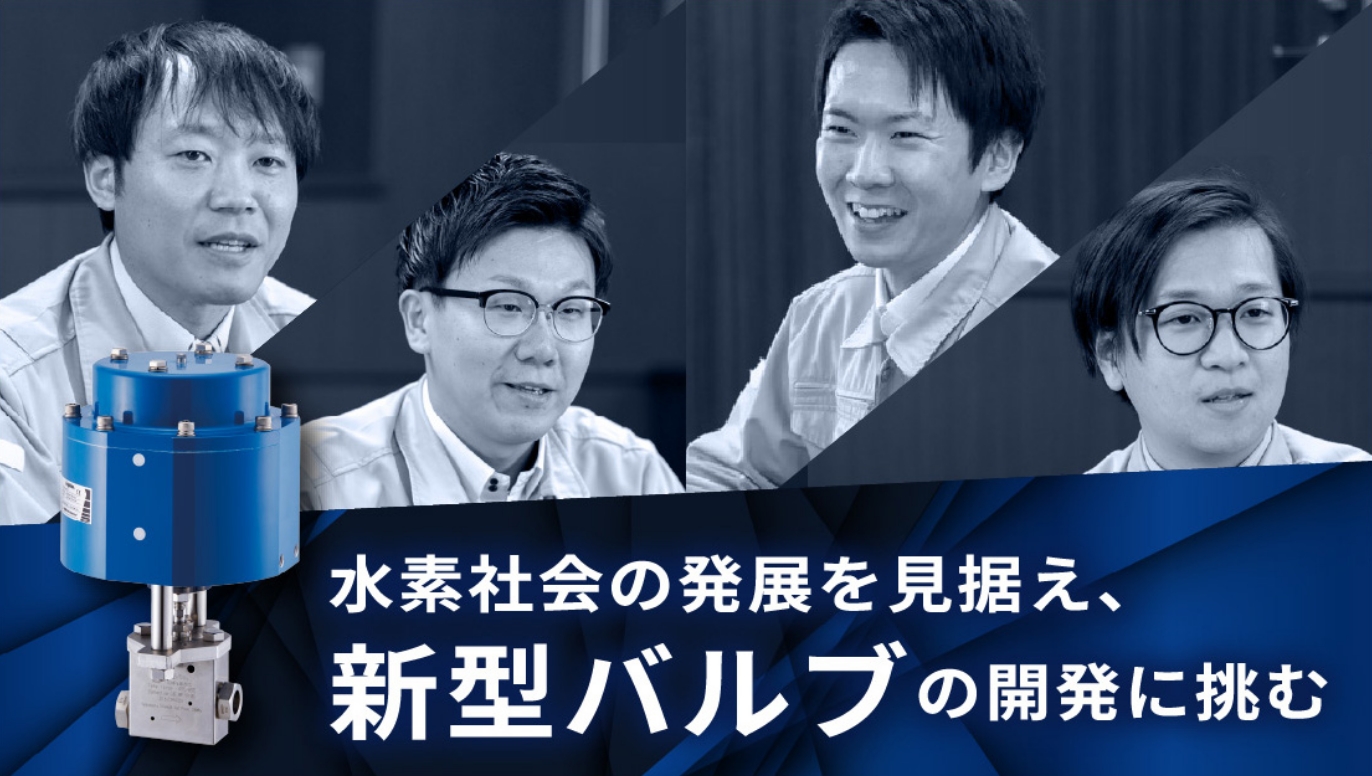
世界的にも例が少ない、
大流量水素ステーション向け
超高圧バルブ機器
トラックや鉄道、建設機械といった大型車両に水素を活用しようという動きが、世界的に広まっています。ただ、従来の水素ステーションで大型車両に水素を充填する場合、長時間かかってしまうという課題があります。そうした中フジキンは、高速で水素充填を可能にする新型バルブを開発。水素活用の可能性を大きく広げるこのバルブはどのような特長を持ち、どう開発されたのか。4人の開発担当者に聞きました。
MEMBER
-
統括
H -
設計
M -
設計
H -
評価試験
K
Chapter 1
半世紀におよぶ
水素技術の蓄積の末に
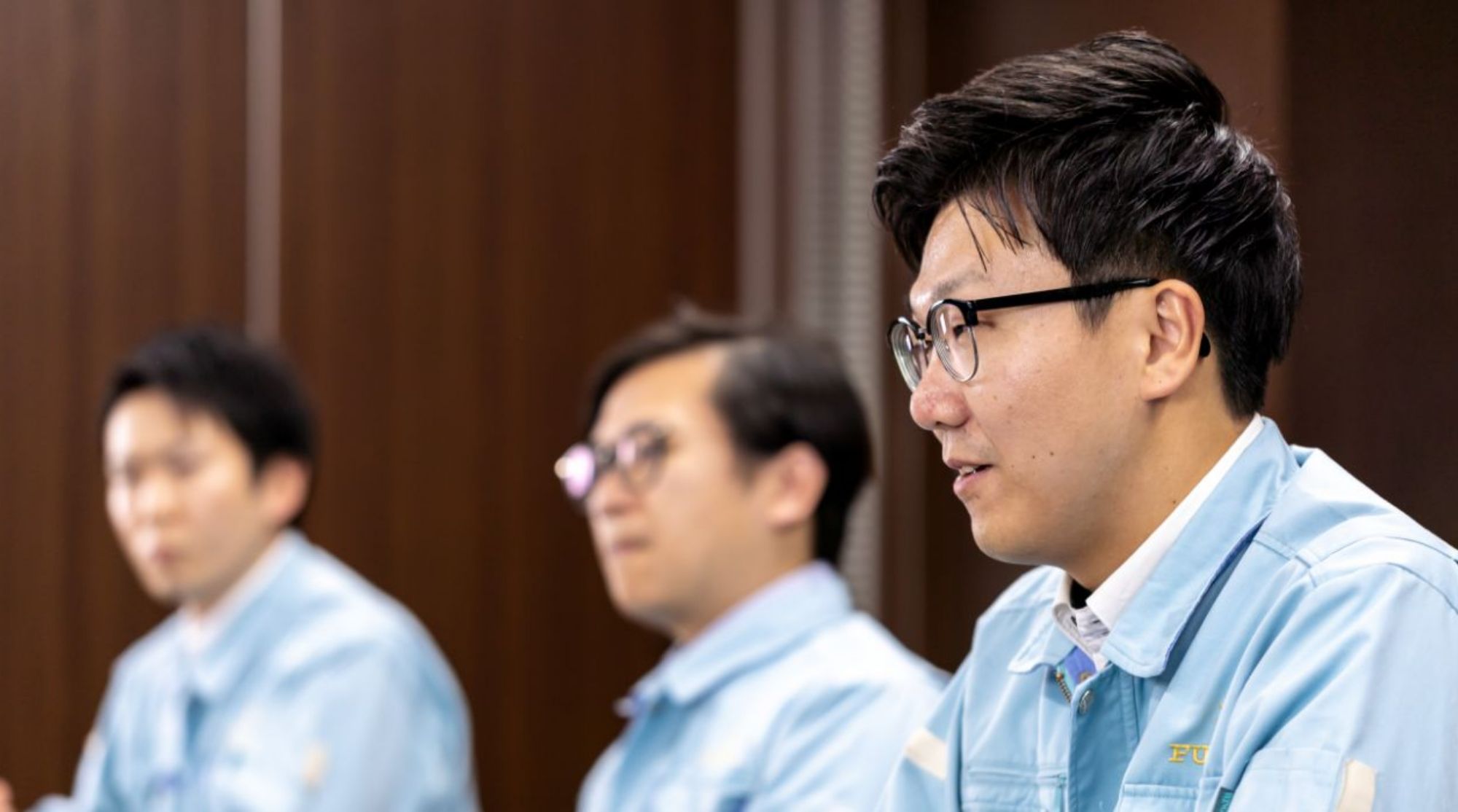
待ち望んだ開発。
だが、期日まではわずか10カ月…
二酸化炭素の削減が喫緊の課題となる中、水素を燃料とする燃料電池車(FCV)の利用が広がっています。しかし、トラックなどの大型車両は多くの水素が必要で、従来の水素ステーションで水素充填すると長い時間がかかり、FCV のメリットの一つである、充填時間の短さが失われてしまいます。
そこで現在、大型・商用モビリティ(HDV)を高速で充填できる大流量水素ステーションの開発が世界的に進んでいます。その背景のもとフジキンでは、2022年に、水素の高速充填に対応する新型バルブの開発に成功しました。
開発の裏には、フジキンの約50年にわたる水素技術の蓄積があります。私たちは1970年代、国産のロケットで初めて水素を燃料としたH-1型ロケットの開発に携わったことから、水素分野への取り組みを始めました。その後、2000年代に入って以降は、水素ステーションの実証設備用のバルブを開発。そして2014年には、国内初の商用水素ステーションにバルブ納入を果たします。現在国内には170の水素ステーションがありますが、その全てにフジキンのバルブが使われています。
そうして蓄積してきた長年の知見から、将来的には大流量の水素ステーションの需要が高まることを予測。その際に必要となる高速充填用バルブを開発する機会を探っていたところ、福島県浪江町に「福島水素充填技術研究センター」が立ち上がることになり、その機会を得ることになります。センターに建設予定の、大流量充填実用化のための評価用実証ステーションのバルブ開発を受注したのです。2020年のことでした。
Chapter 2
新型バルブが実現すべき
3つのポイント
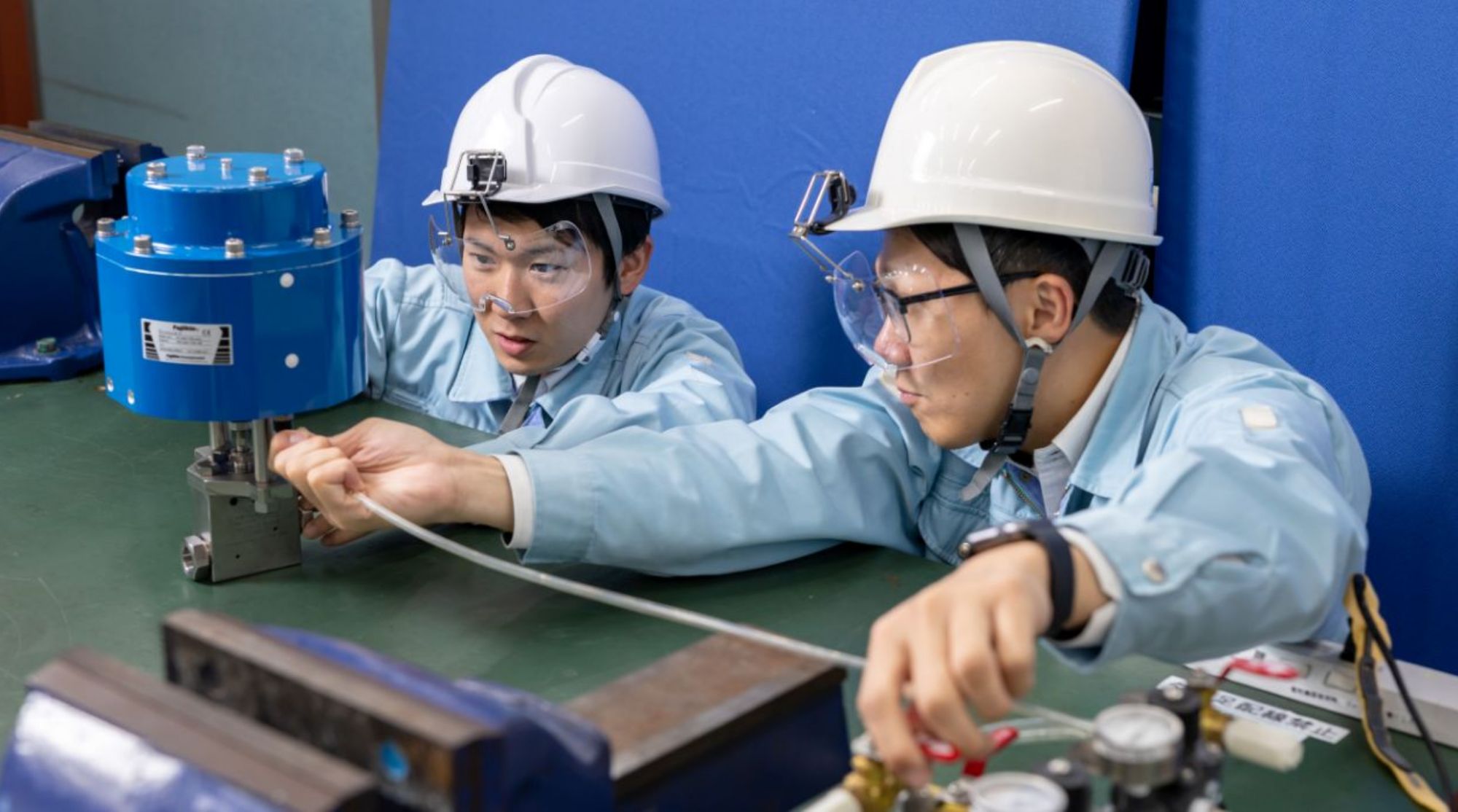
設計・試作・試験の3工程を、
ほぼ同時に進行した。
大流量水素ステーション向けの新型バルブを開発する上で、実現すべき点は大きく3つありました。
1つ目は、一番の目的である大流量化です。HDV に搭載される水素の量は40kg(海外仕様は80kg)で、FCV(5kg)の8倍以上。そのため、現行のFCV向け水素ステーションでHDVに充填しようとすれば、FCVは約3分なのに対して、HDVは約22分かかってしまいます。その充填時間を短縮するため、流量を約2.5倍にすることを目指しました 。「2.5倍」という値は、製品の主要なターゲットであるアメリカやヨーロッパで求められる流量に沿って決められました。
2つ目はバルブのコンパクト化。バルブは、開閉操作を行う「駆動部」と、バルブ本体となる「本体部」に分かれますが、バルブを大流量化するためには、駆動部が大きな推力を出せることが必要です。ただそのためには、駆動部の直径がどうしても大きくなり、結果、バルブ全体も巨大化します。実際に水素ステーションに設置することを考えると、できるだけコンパクトにすることが求められます。
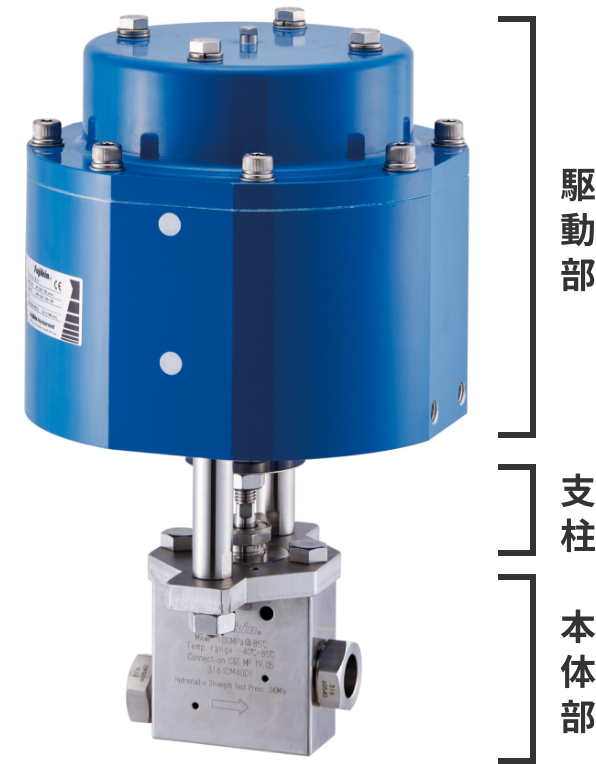
開発した大流量タイプの遮断弁
そして3つ目は信頼性の向上です。取り扱う水素の量が大きくなるため、安全性にはより留意する必要があり、加えて、高い耐久性を持たせることも目指しました。
ではその開発は、どう進んでいったのか――。
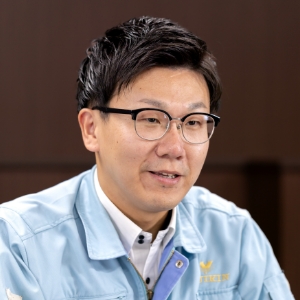
統括 H
開発の工程は、設計、試作、試験の3段階に分かれます。通常は、設計、試作の後に試験を行って課題を見つけ、また設計、試作に戻るということを繰り返します。が、今回は時間的余裕がなかったため、様々な工夫が必要でした。駆動部ができたらまずそちらだけ先に試験を行うなどして、3つの段階をできるだけ並行して進めました。
Chapter 3
大流量化、コンパクト化を
実現するための方法とは
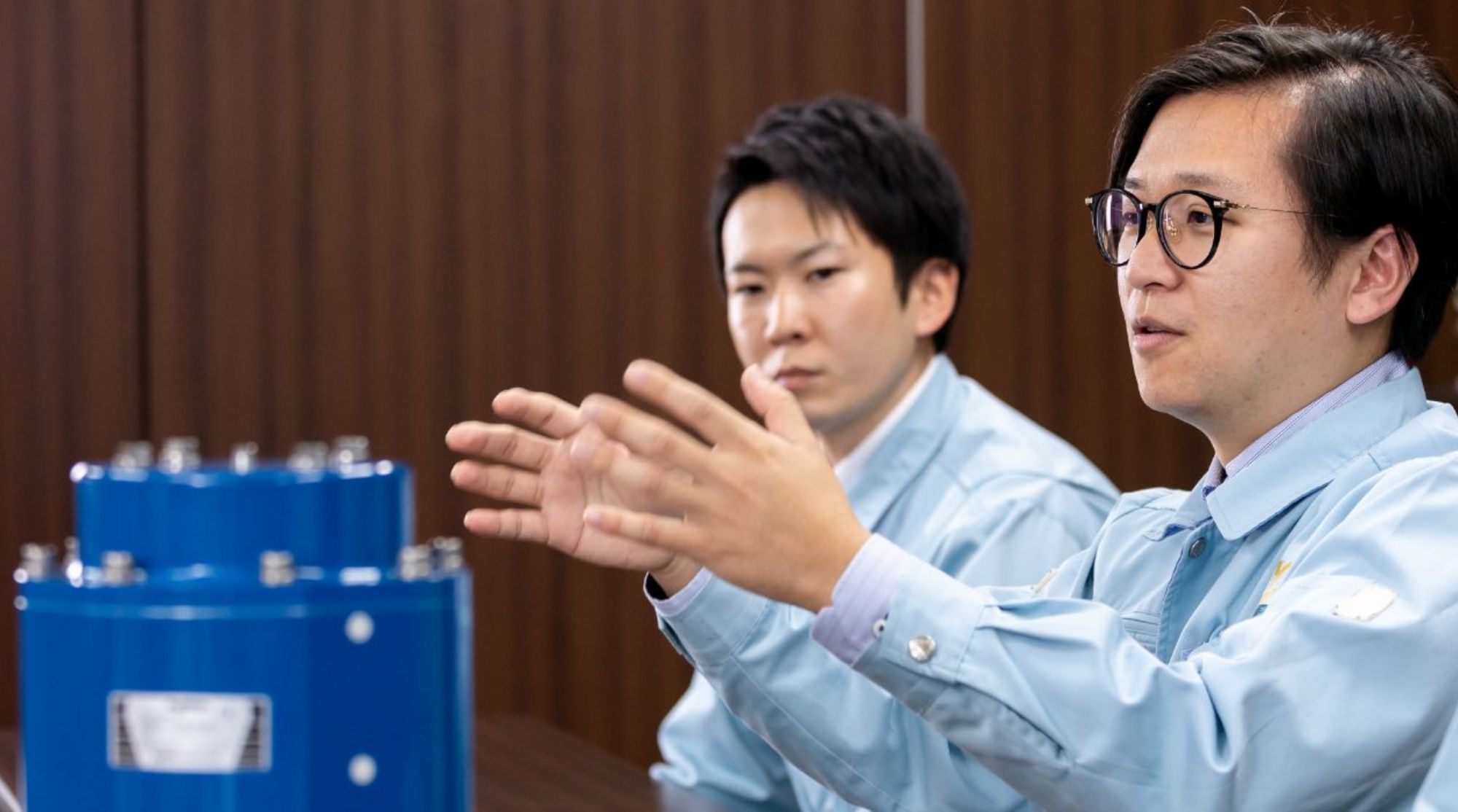
ゼロからの設計は初めて。重圧の中、試行錯誤しながら発想を形に。
設計を任されたのは、当時入社4年目のH(設計)でした。
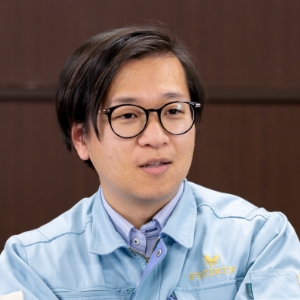
設計 H
私にとって設計をゼロから任されるのは初めてのことでした。その上、設計すべき機器は、メインのバルブに加えて、手動のバルブ、不純物除去のためのフィルター、逆流防止のための逆止弁と計4つ。時間も限られていて、重圧がかかる中でのスタートになりました。
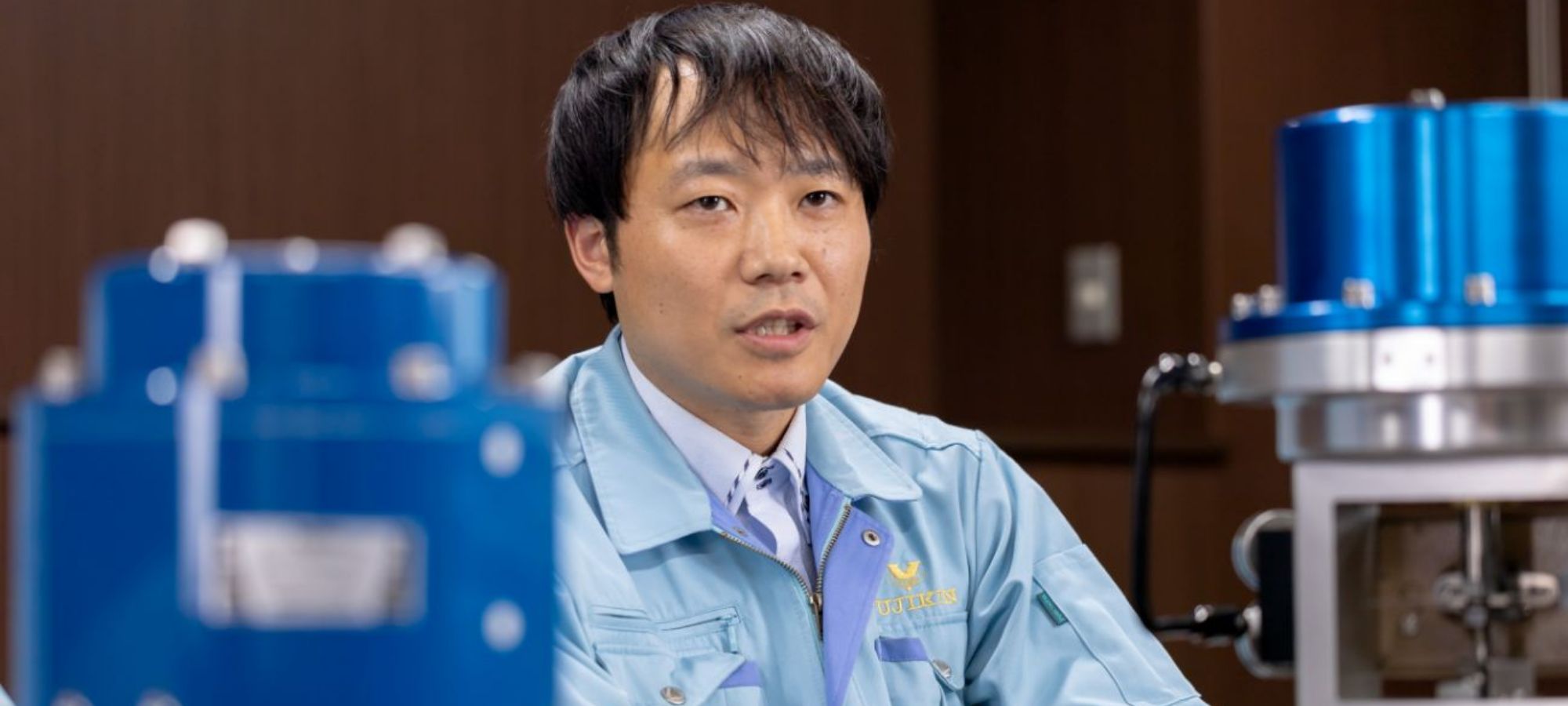
現地で培った多くの経験と知見が、
コンパクト化実現の鍵に。
H(設計)は最初の数カ月、この設計にかかりきりに。流路内径を大きくするなど、従来の水素充填バルブに工夫と改良を加える形で図面を描き進めていきました。その中で、特にポイントとなったのは、駆動部に「ダブルピストン」という構造を採用したことでした。
駆動部は、ピストンによって本体部に力を伝えることでバルブの開閉を行いますが、その際、ピストンの面積が大きいほど推力が増します。単純に言えば、面積が2倍になれば推力も2倍になり、その結果、流量を大きくできる。しかし一方、ピストンの面積を大きくすれば、駆動部が横方向に大きくなってしまいます。つまり、大流量化を目指すとコンパクト化が困難になってしまうのですが、その問題を解決するのがダブルピストン構造です。ピストンを縦に2枚配置して、合計の面積を縦方向に大きくすることで推力を高めます。
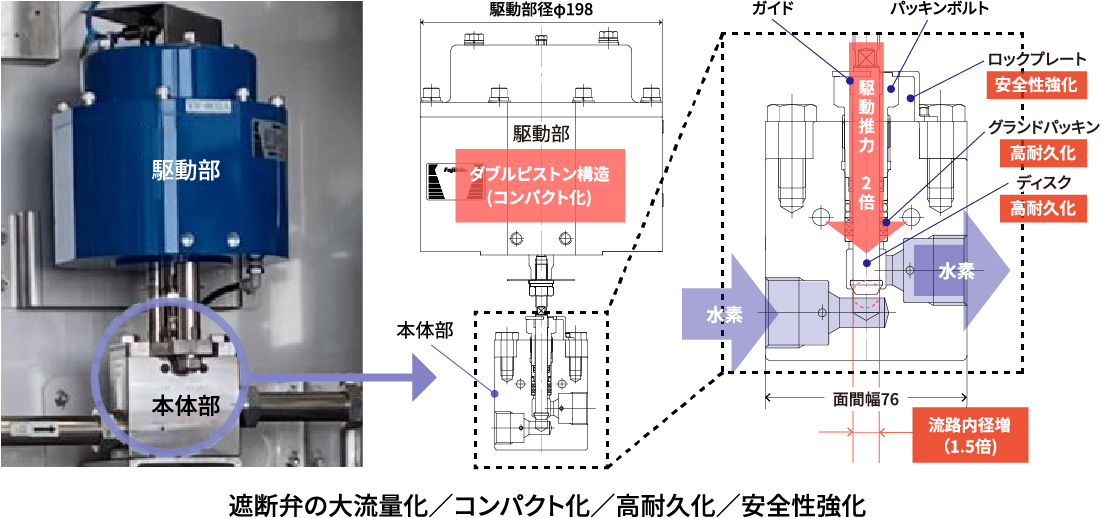
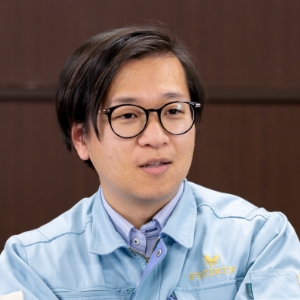
設計 H
構造が複雑になるのでチャレンジではあったのですが、自分で考えてもうまくいかないところは、設計の経験が豊富なH(統括)さんやM(設計)さんに相談しながら進めていきました。先輩たちのサポートに助けられながら、なんとか形にすることができました。
大流量化とコンパクト化を両立できるこの構造を採用した結果、駆動部の直径は、従来の水素ステーション用バルブの直径と比較して、10%程度の増加に抑えることができました。
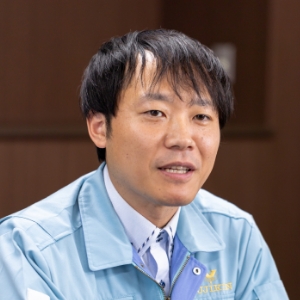
設計 M
H(統括)さんや私は、実際に水素ステーションを現地で見て、作業をしてきた経験も多くあります。そのため、バルブが横方向に大きくなると設置の際に難しさが生じる可能性があることは、理解できていました。そうした知見が、ダブルピストン構造を採用しようという発想へとつながりました。
Chapter 4 完成間近に、支柱が折れる――
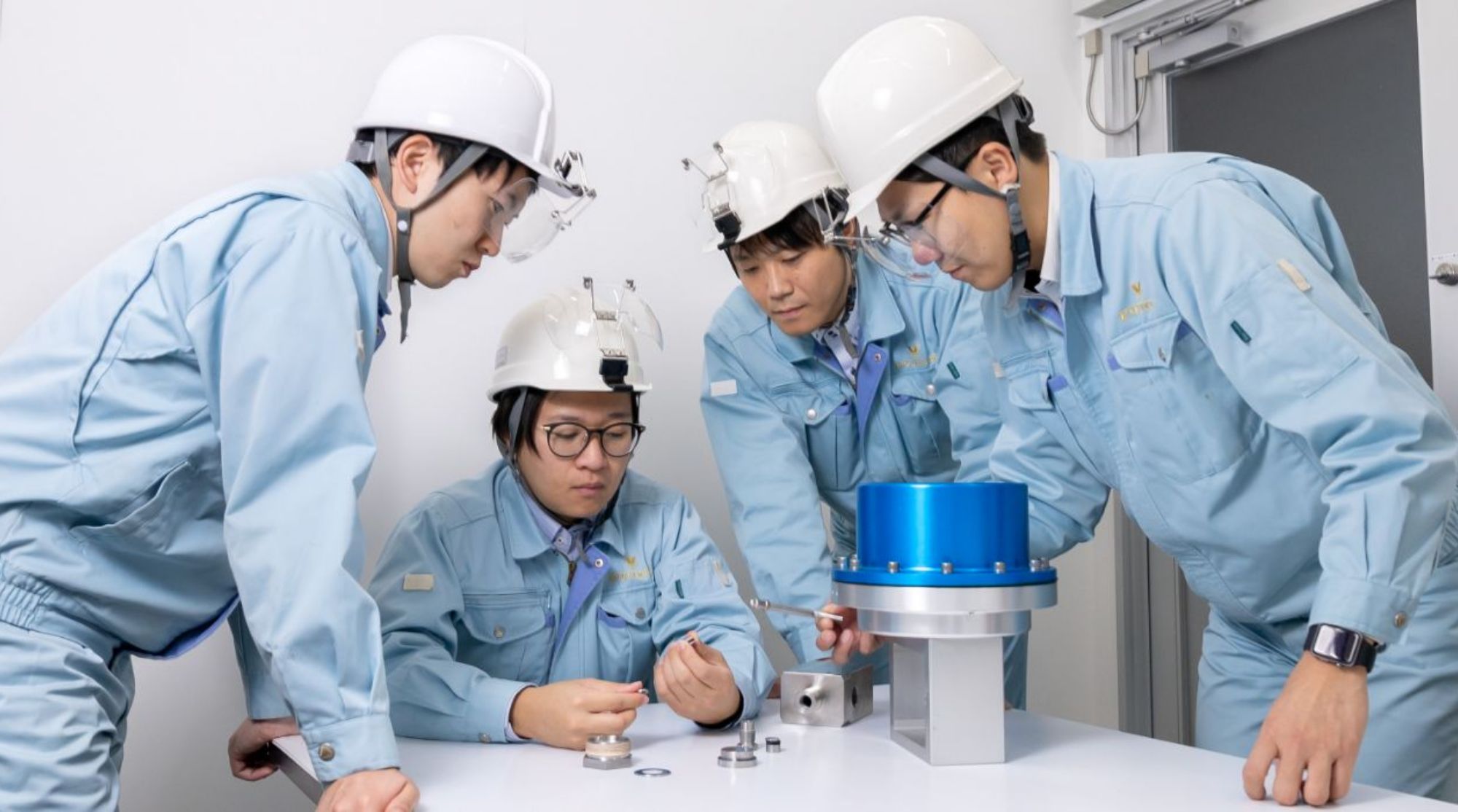
続くトラブル。そのたびに知恵を出し合い解決策を探った。
設計は比較的順調に進みましたが、その後に続く試作、試験の段階では複数のトラブルが発生し、そのたびにメンバーで話し合い、一つずつ解決していきました。
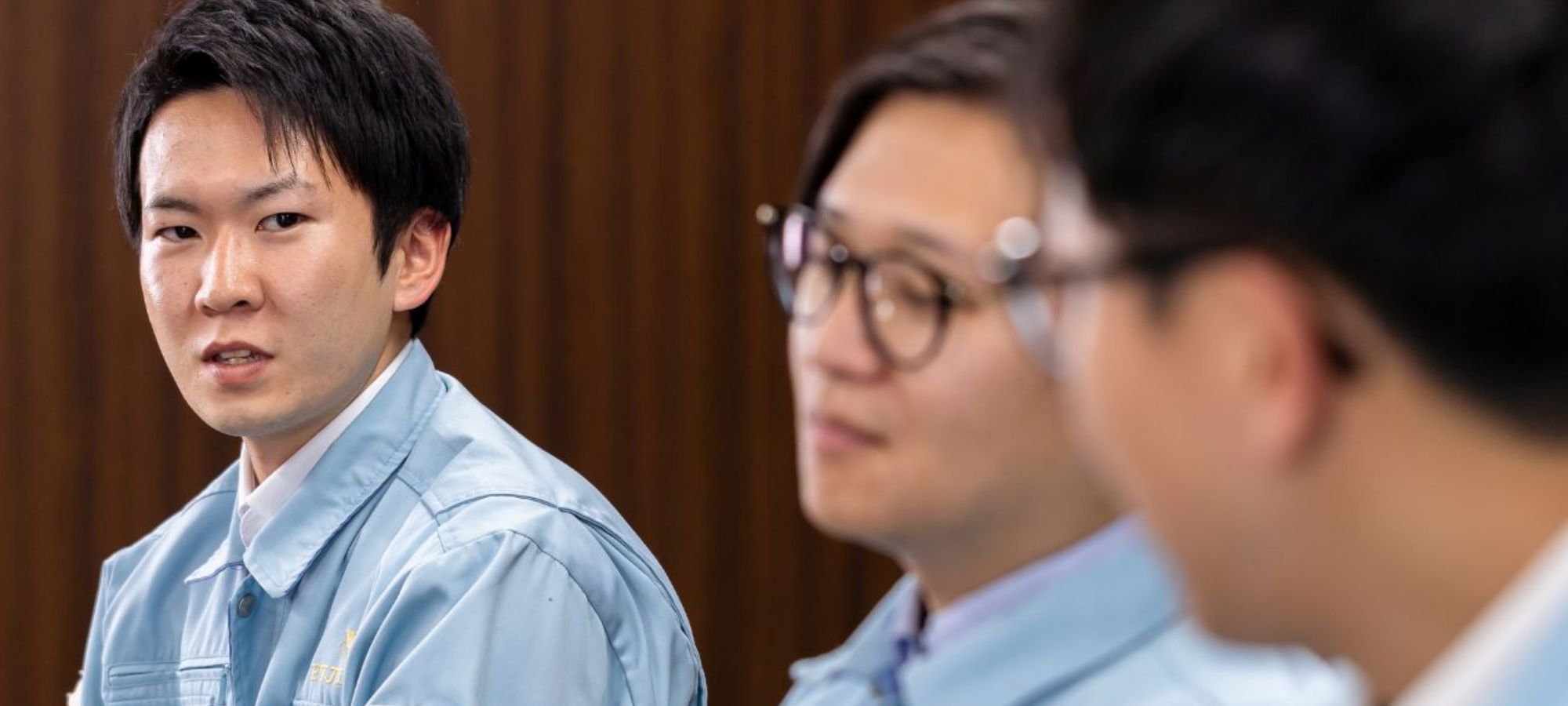
支柱が折れた―。最終局面で発生した最大のトラブル。
そうしてようやくバルブ全体が出来上がり、これでいよいよ完成か、というタイミングで思わぬトラブルが再び発生しました。
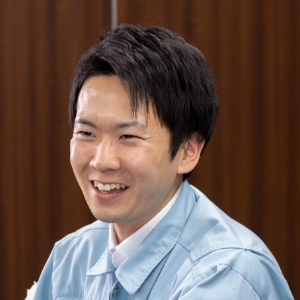
評価試験 K
耐久性を評価するためにバルブを繰り返し開閉する試験をしていたときのことでした。バルブの開閉を7万回、8万回と繰り返すうちに、駆動部と本体部を接続する支柱の1本が折れてしまったんです。
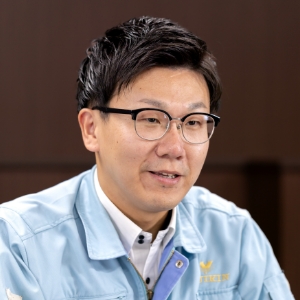
統括 H
私は出張中だったのですが、電話で「折れました」と聞いて驚きました。「うそやろ?」って。でも、写真を送ってもらって見たら、本当に折れていました…。
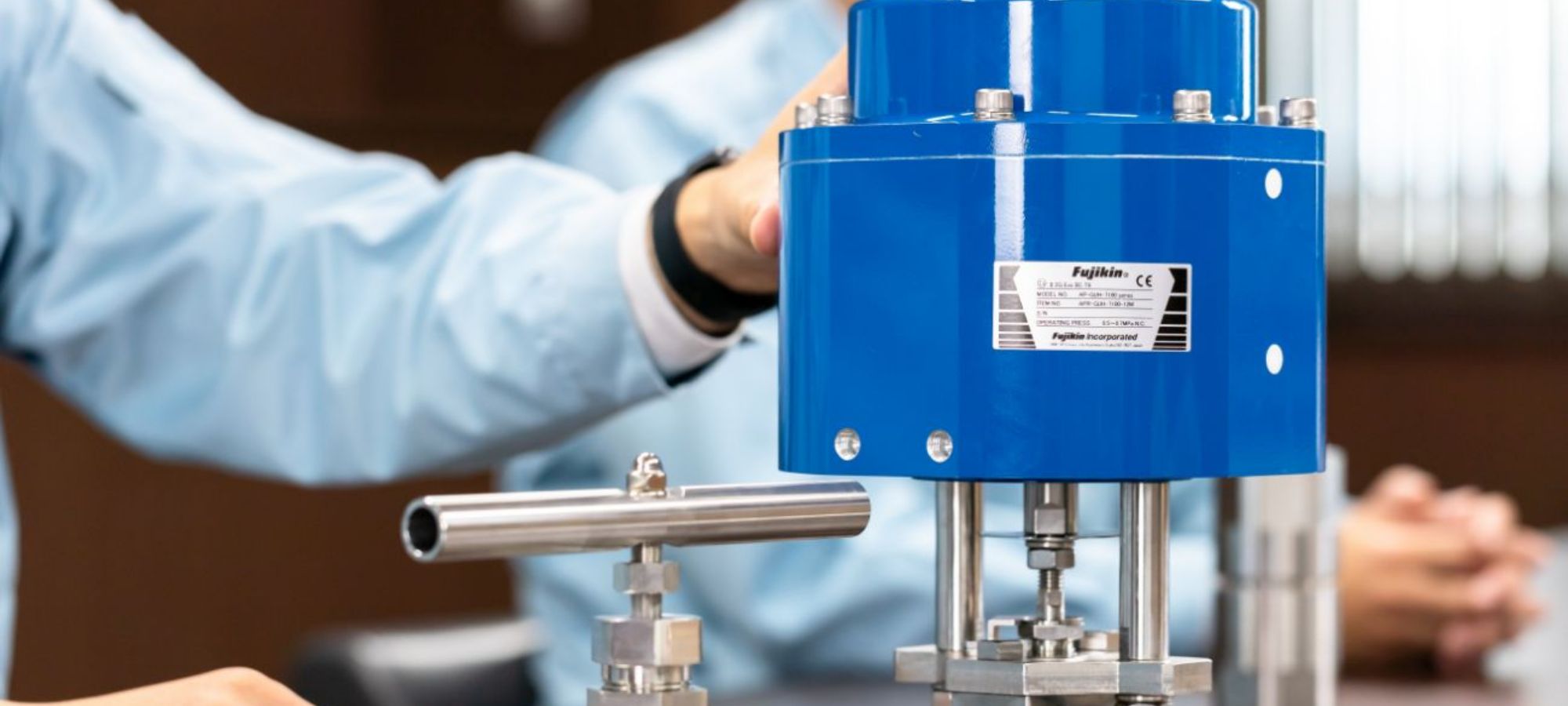
ISOに準拠する評価試験の基準を
大きく上回る耐久性に。
配管の中を流れる流体には100MPa近い圧力がかかっています。100 MPaとは、1㎠の領域に1トンの荷重がかかるほどの力です。それをバルブで止めるので、駆動部には想像を絶する強い力がかかります。
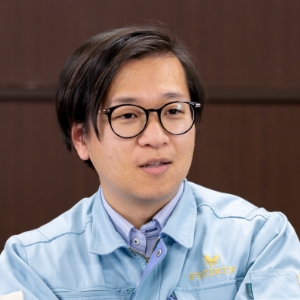
設計 H
折れた破面を分析して、どのような力がかかったのかを考えました。そして形状を修正して、再度試作。しかしまた失敗でした。そこでもう一度作り直し、3回目の試験のとき、ようやくすべてをクリアすることができました。
期日が迫る中、なんとか完成。綱渡りのような工程でしたが、最終的なクオリティは満足できるものに。ISOに準拠する評価試験を行うと、基準を大きく上回る耐久性が確認できました。
水素ステーションで使用されるバルブには、合計10万2000回の開閉耐久サイクルが求められ、その際、1万6000回ごとにシール部品を交換することが認められています。
しかし、開発したバルブは、シール部品の交換を一度も行うことなく、10万2000回の試験を合格。最終的には、目指していた点をすべて満たすバルブを完成しました。
Chapter 5
受賞、そして
それぞれが得たものは
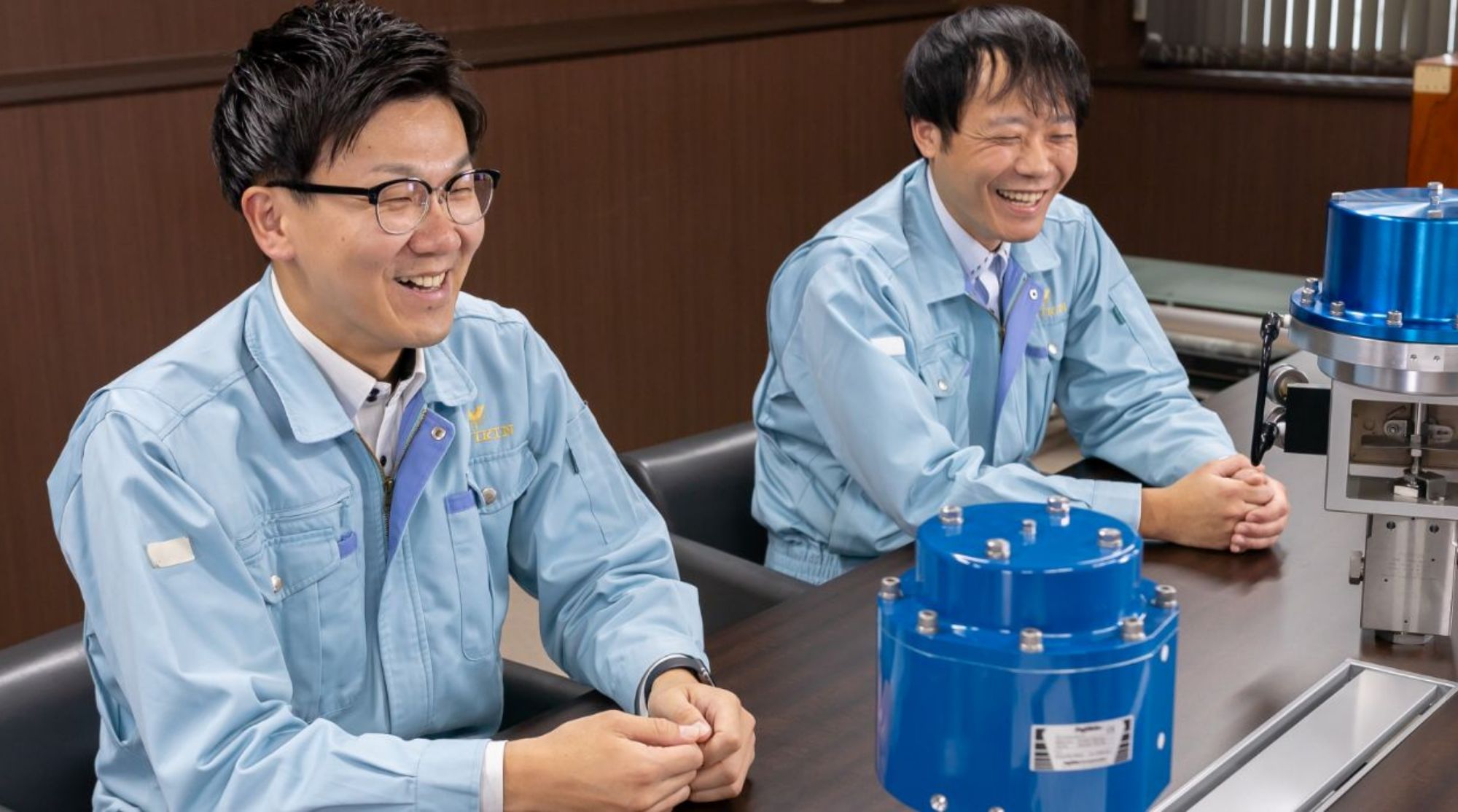
世界でも例が少ない新バルブ製品に、海外からも「使ってみたい」の声。
上記のバルブと付随する3つの機器を含めた4つのバルブ機器は2021年6月に完成、福島水素充填技術研究センター様に納品されました。商用の大流量水素ステーションに必要になるもう一つのバルブ(調節弁)も翌2022年には完成し、計5つのバルブ機器が、「大流量水素ステーション向け超高圧バルブ機器」として、2022年4月に販売開始。そして2023年、第20回 超モノづくり部品大賞において、「モビリティー関連部品賞」を受賞しました。
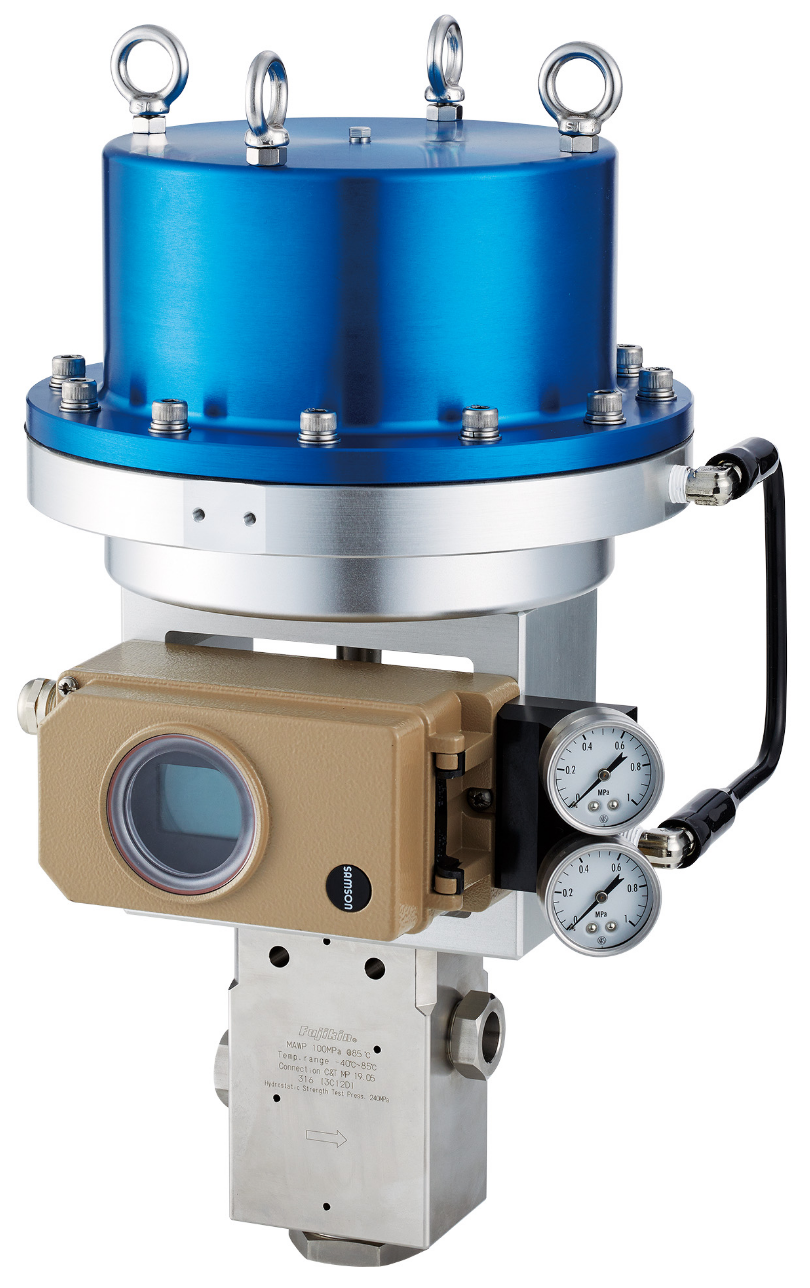
大流量タイプの調節弁
アメリカやヨーロッパでHDV向け水素ステーションの開発は進んでいるものの、本製品のようなバルブは、世界的にもほとんど例がありません。「使ってみたい」という声が海外からも多く届いています。そうした反応が得られる製品を作り上げられたことは、開発メンバーそれぞれにとって、大きな喜びであり、次につながる経験となりました。
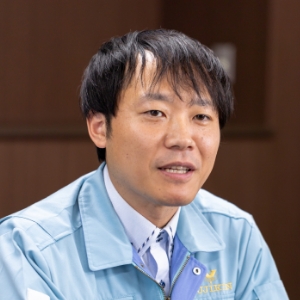
設計 M
調節弁の設計を担当し、他の4つの機器からは少し遅れての完成となりましたが、このチームのみんなとともに、世界に広く求められる製品を完成させられたことをすごく誇らしく思っています。
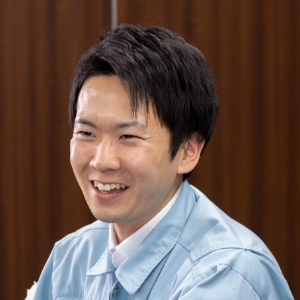
評価試験 K
当時まだ入社3年目くらいでしたが、この製品の評価試験においては様々な仕事を任せてもらえ、成長の機会となりました。試験、改良を繰り返す中で、性能がどんどん良くなっていく過程を間近で見られたことは、今後自分で設計をしていく上で、きっと活きると思っています。
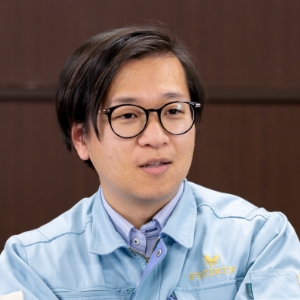
設計 H
ゼロから4つの機種を設計するというのは初めての経験で、プレッシャーはとても大きかったですが、最後までやり切ることができ、大きな自信になりました。今回の経験を活かして、これからもどんどんチャレンジをしていきたいです。
そして、この3人を主軸とする開発全体を統括したH(統括)は、今回の開発においてはとりわけ、世界を強く意識する経験を得ました。
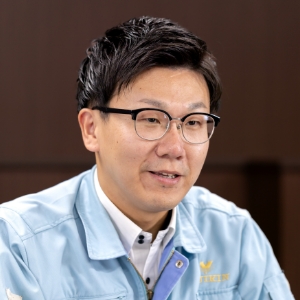
統括 H
本製品の主要なターゲットがアメリカやヨーロッパだったため、開発前に海外の情報を精査することなどにかなり力を注ぎました。国・地域ごとに要求が異なる中、いかに広く世界に求められる製品を作るかを考えることは私にとって大きな学びになりました。今後ますます世界を意識しながら、フジキンならでは製品を開発していきたいです。
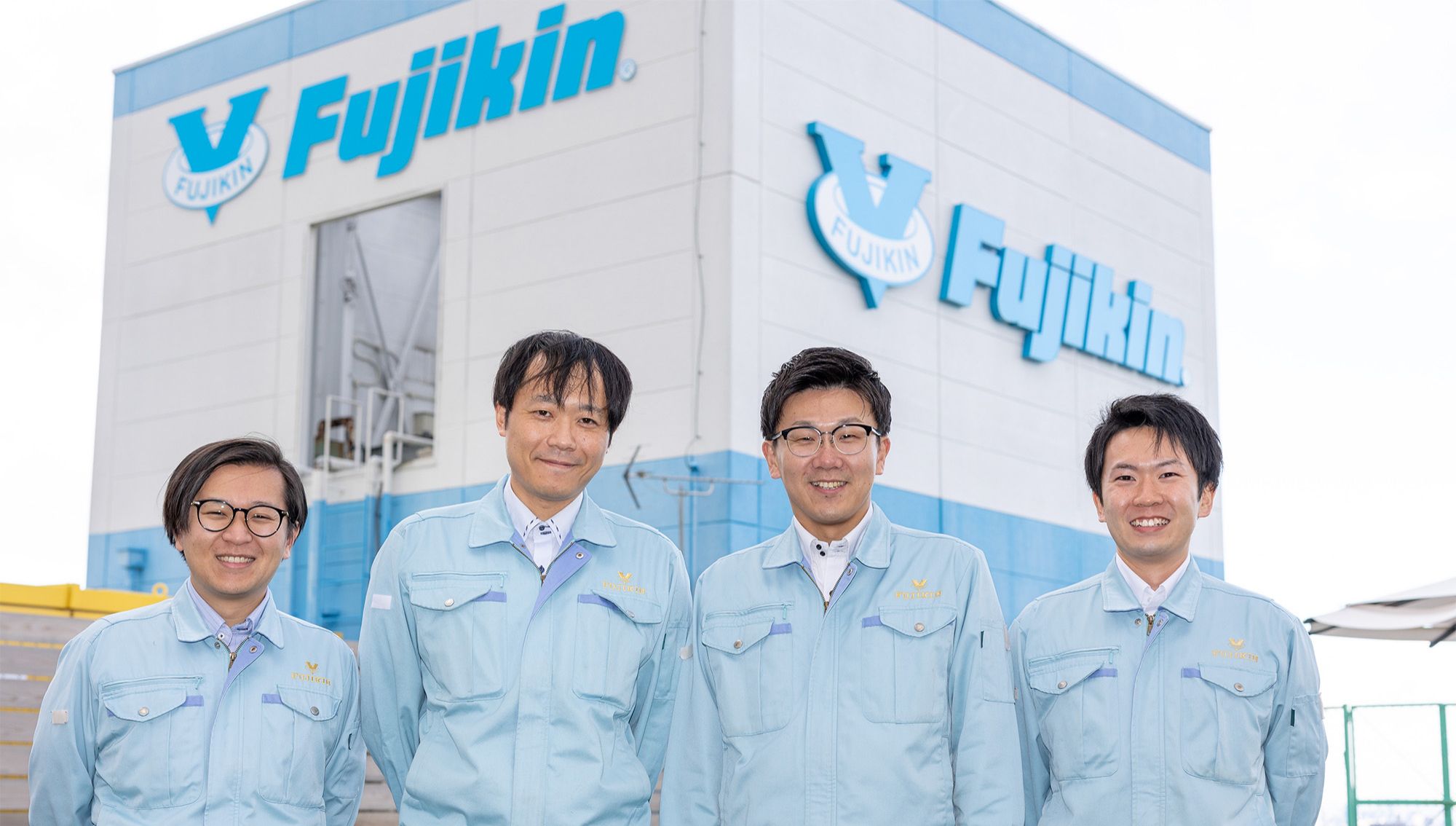
※取材内容、および登場する社員の所属はインタビュー当時のものです。
関連リンク
大流量水素ステーション向け超高圧バルブ機器
統括 H
開発することが決まった時、期日まではすでに10カ月ほどしかありませんでした。与えられた時間が短く、プレッシャーは大きかったのですが、とにかくやろうと、すぐにメンバーを決めて着手しました。